Capacitor Discharge (CD) welding is a specialized welding technology that plays a pivotal role in various applications where precise, rapid, and high-integrity bonds are required. This process is especially valuable for electrical and structural engineers working with thin or conductive materials where minimal heat distortion is paramount. Below, we provide a detailed exploration of the CD welding process, the principles that govern it, the equipment involved, and its distinct advantages over other welding methods.
The Principles of Capacitor Discharge Welding
At its core, CD welding operates on the principle of rapid energy release to create a strong and localized weld. The technology employs capacitors—devices that store electrical energy—to discharge this energy within milliseconds. Here’s how the process unfolds:
Energy Storage: The capacitors are charged to a pre-set voltage, depending on the material properties, required weld strength, and desired penetration.
Energy Discharge and Fusion: Upon initiation, the stored electrical energy is rapidly discharged through an electrode. This causes an intense but short-lived heat generation at the interface of the materials being joined.
Material Bonding: The heat melts a small volume of the material at the contact point. Simultaneously, the electrode applies pressure, ensuring that the molten material fuses seamlessly as it cools and solidifies.
This ultrafast energy release ensures localized heating, significantly reducing the heat-affected zone (HAZ) and any risk of distortion or damage to adjacent components. The method is ideal for delicate or thin conductive materials such as those used in electronic components, precision fabrication, and structural fasteners.
Essential Equipment in CD Welding
CD welding relies on specialized machinery designed to execute the process with precision and consistency. Some of the key components include:
Capacitor Bank:
This component forms the backbone of the system. Capacitor banks store the high electrical energy required for the discharge. The size and capacity of the bank determine the system’s ability to weld thicker materials.
Power Supply:
The power supply charges the capacitor bank. Modern systems often incorporate adjustable settings to adapt to various operating conditions and material properties.
Welding Head:
The welding head houses the electrode and applies pressure to the weld area. Many designs allow precise customization of electrode force to ensure optimal bonding.
Control Unit:
The control unit governs essential parameters, including voltage, discharge time, and electrode alignment. Advanced models incorporate programmable logic controllers (PLCs) that enable operators to store multiple welding programs for efficiency and repeatability.
Electrodes:
The electrodes are the contact points through which energy transfers to the materials. They play a critical role in the overall quality of the weld. Due to their heat and electrical conductivity properties, tungsten or copper-tungsten electrodes are common.
Advantages of Capacitor Discharge Welding
CD welding stands out among other welding techniques for its unique set of advantages. Below are reasons why this method is well-suited for both electrical and structural engineering applications:
1. Speed and Efficiency
The entire welding process typically completes in milliseconds. This allows for high throughput in production environments, making it ideal for industries requiring mass production of precision components.
2. Minimal Heat-Affected Zone (HAZ)
One of the defining characteristics of CD welding is its ability to localize heat generated during the process. This minimizes thermal distortion, ensuring the integrity of heat-sensitive materials or assemblies.
3. Compatibility with Thin Materials
Unlike traditional fusion welding techniques, CD welding excels with thin materials without burning or tearing. It is frequently used for attaching metal fasteners, wire terminals, and thin sheets in electronics and aerospace applications.
4. Material Versatility
CD welding is compatible with a wide range of materials, including stainless steel, aluminum, copper, and various alloys. Some systems also support dissimilar material joints, a significant advantage in engineering projects requiring hybrid assemblies.
5. Eco-Friendly
The short process duration and reduced energy consumption make CD welding an environmentally friendly option compared to conventional methods that require sustained energy input.
6. Precision
The process ensures repeatability and consistency for high-precision applications. Engineers can control energy discharge down to the millisecond, ensuring welds meet stringent quality standards.
Applications of CD Welding in Engineering Fields
Capacitor Discharge welding is indispensable in both electrical and structural applications. Below are a few industry-specific use cases:
-
Electrical Engineering:
- Creating secure connections in circuit components
- Attaching terminals to battery systems
- Welding busbars and conductive sheets
-
Structural Engineering:
- Joining metal fasteners like studs and pins to thin structural components
- Achieving high-strength bonds in assemblies without weakening the base material
These applications highlight the versatility and importance of capacitor discharge welding in modern engineering disciplines.
Final Thoughts
Capacitor Discharge welding represents a highly efficient and precise method for joining materials in various engineering sectors. By understanding the principles, equipment, and advantages of CD welding, electrical and structural engineers can leverage this technology to achieve superior results in their projects. Whether working on microelectronics or structural assemblies, this method provides a high-quality solution to meet functional and production demands.
For engineers ready to explore or optimize CD welding, collaborating with an experienced services provider ensures access to the latest equipment and expertise required for challenging applications. The right partner will help you unlock the full potential of this cutting-edge welding technique.
Explore More on Welding Technologies
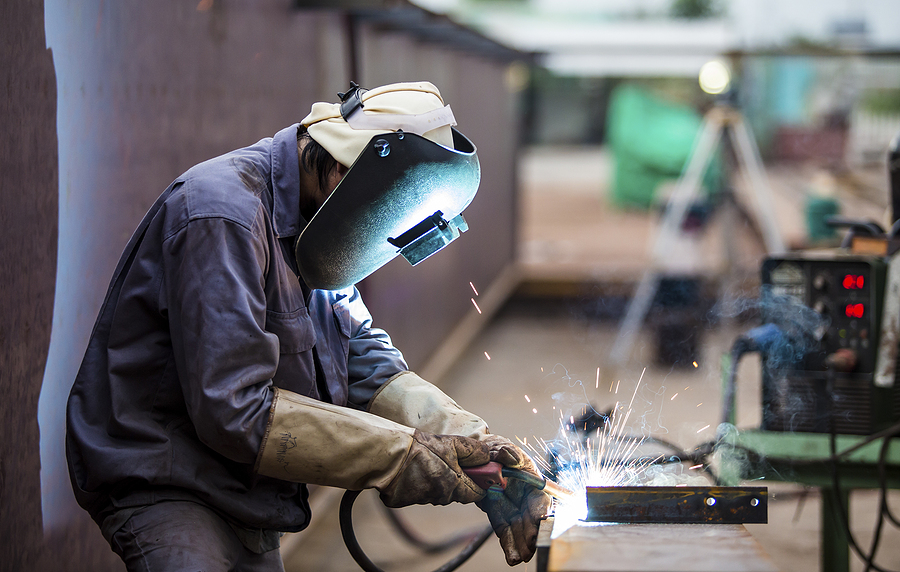
PECo Welding Solutions Expands into MIG and TIG Welding Services
At Process Equipment Company Welding Solutions (PECo), we’re always searching for new ways to serve our community and industry partners. We’re thrilled to announce that PECo is now offering traditional MIG and TIG welding services as part of our growing portfolio....
Capacitor Discharge Welding in Modern Engineering: Applications and Innovations
Capacitor Discharge (CD) welding has become a versatile and efficient welding technique in modern engineering. Its precision, speed, and ability to work with thin materials make it indispensable across industries from electronics to aerospace and construction. Over...
Ensuring High-Quality Results in Capacitor Discharge Welding: Tips from Industry Experts
Capacitor Discharge (CD) welding is a go-to technique for applications requiring precision bonding, minimal heat distortion, and compatibility with thin or conductive materials. While the process itself is highly efficient, maintaining consistent, high-quality results...
Preparing Metals for Capacitor Discharge Welding: Best Practices for Engineers
Capacitor Discharge (CD) welding is revered for its precision and efficiency, especially in scenarios involving thin or conductive materials. However, the quality of the weld is heavily influenced by how the materials are prepared beforehand. For electrical and...
Get Expert Guidance on Capacitor Discharge Welding
Reach out to Process Equipment Company today to learn more about our specialized welding services. Whether you need detailed information or a personalized quote, our team is ready to assist you with all your capacitor discharge welding needs.