Capacitor Discharge (CD) welding has become a versatile and efficient welding technique in modern engineering. Its precision, speed, and ability to work with thin materials make it indispensable across industries from electronics to aerospace and construction. Over the years, advancements in CD welding technology have expanded its scope, offering innovative solutions for complex engineering challenges.
This article examines the diverse applications of CD welding across critical industries and highlights recent technological innovations driving its adoption.
Applications of CD Welding in Engineering
CD welding’s precise energy delivery and rapid process cycle make it an ideal choice for joining components in industries where quality and efficiency are paramount. Here’s how it’s being applied today:
1. Electronics Industry
The electronics sector demands precision and minimal heat impact, making CD welding the go-to solution for many applications. Components in this sector are often sensitive to thermal distortion, requiring localized and controlled heat application.
- Battery Terminals:
CD welding is extensively used to connect battery terminals, ensuring strong electrical conductivity while preventing excess heat from damaging the cells. - Circuit Fabrication:
Electrical contacts and busbars within circuits are securely welded using CD welding, allowing for small yet durable bonds. - Connector Assembly:
Joining wire terminals or attaching connectors to metal pads is another common use. This process ensures stable connections with the high repeatability critical to mass production.
2. Aerospace Industry
The aerospace sector’s emphasis on lightweight and high-strength materials aligns perfectly with CD welding’s capabilities. Using this technique allows engineers to join dissimilar metals with minimal impact on their structural integrity.
- Fastener Attachment:
Attaching pins, studs, or bolts to thin aluminum panels or titanium components is seamless with CD welding. The process minimizes the risk of warping, which is essential for maintaining aerodynamic properties. - Sensitive Equipment Assembly:
Components housing delicate sensors or electrified systems rely on CD welding to prevent thermal damage while creating robust joints. - Weight Reduction:
The ability to weld thin or dissimilar materials ensures lightweight assemblies, meeting stringent performance requirements.
3. Construction and Structural Engineering
Structural engineering applications often require welding anchors, studs, or connectors onto large metal frameworks. CD welding delivers speed and consistency even when working on uneven or angled surfaces.
- Metal Stud Welding:
CD welding simplifies the installation of structural fasteners like threaded studs or bolts onto beams, girders, and wall panels. The process is faster than traditional arc welding and produces minimal spatter. - Facade Assembly:
The technique is used for fixing cladding or curtain-wall support brackets to structural elements, ensuring durable and aesthetic assemblies. - Bridge Restoration:
Dissimilar metal bonds required for repair and modernization projects are achieved with precision, enabling structural integrity without overhauling existing designs.
4. Medical Equipment Manufacturing
The medical field requires the fabrication of precision instruments and devices where quality standards are unyielding. CD welding is well-suited for materials like stainless steel and titanium used in medical-grade tools.
- Surgical Instruments:
Welding fine stainless-steel components with minimal discoloration ensures high tolerances and retains corrosion resistance, essential for sterilization. - Implant Assembly:
Titanium implants, designed for biocompatibility, are joined using CD welding to reduce residual stress and enhance durability, critical for long-term use inside the human body.
5. Automotive Industry
Automakers have increasingly turned to capacitor discharge welding for lightweight designs and improved energy efficiency.
- Electrical Systems:
Specialized busbars and connectors within hybrid and electric vehicles (EVs) are assembled using CD welding for superior electrical conductivity. - Body Assemblies:
Joining dissimilar materials such as aluminum and steel contributes to stronger yet lighter vehicle frames, which is critical for fuel efficiency.
Recent Innovations in Capacitor Discharge Welding
Technological advancements have reshaped CD welding, broadening its potential applications while improving its performance. Here are some of the leading innovations shaping this field:
1. High-Power Controllers
Modern CD welding systems feature high-power controllers that allow better energy management. These innovations enable engineers to accurately tailor discharge voltage and timing to match challenging projects, such as welding extremely thin materials or combining alloys with disparate thermal properties.
2. Programmable and Adaptive Systems
Programmable logic controllers (PLCs) and advanced user interfaces have made CD welding equipment more intuitive. Adaptive systems automatically adjust parameters in real-time based on input from sensors monitoring:
- Conductivity
- Material thickness
- Ambient temperature
This adaptability reduces setup time and increases repeatability in production environments.
3. Micro-Welding Capabilities
Demand for miniaturized and intricate components in industries like electronics and medical devices has driven advancements in micro-CD welding. These systems focus on sub-millimeter-sized contacts, enabling ultra-precise energy bursts and weld profiles.
4. Hybrid Welding Integration
Innovators are exploring hybrid systems that integrate CD welding with other techniques such as laser welding or ultrasonic bonding. These combinations deliver enhanced flexibility for complex projects requiring varying degrees of energy application and weld strength.
For example, combining CD welding with laser welding is particularly advantageous when joining dissimilar metals. The laser can preheat the metal surfaces, enhancing the discharge’s effectiveness for unique material pairings.
5. Eco-Friendly Advancements
As environmental concerns grow, manufacturers are redesigning CD welding systems to reduce their carbon footprint. Energy-efficient capacitor designs, combined with software optimization for lower energy consumption during standby, contribute to smaller environmental impacts. Additionally, CD welding’s inherent low energy expenditure compared to long-duration fusion welding techniques makes it a sustainable option.
6. Data Analytics in Quality Control
Modern CD welding machines have data-logging features that track every weld’s parameters—voltage, pulse width, current, and timing. This data can be analyzed using predictive analytics to optimize future welding cycles and preemptively address potential issues, ensuring higher reliability.
The Future of Capacitor Discharge Welding
Capacitor discharge welding continues to evolve as manufacturers seek faster, greener, and more efficient fabrication methods. Emerging use cases, such as creating modular assemblies for renewable energy systems and advanced robotics, are expanding its impact. Collaboration between manufacturers and engineers will likely lead to even more sophisticated systems optimized for tomorrow’s challenges.
Final Thoughts
Thanks to its speed, precision, and adaptability, capacitor-discharge welding has proven invaluable across diverse industries. Whether improving electrical connectivity in cutting-edge electronics or producing structural assemblies in aerospace and construction, CD welding continues to meet and exceed the exacting standards of modern engineering. With advancements in energy control, micro-welding, and hybrid integration, this technology is poised to address the increasingly complex demands of today’s industry while paving the way for innovative applications in the future.
Engineers and manufacturers must stay informed about these advancements to fully utilize CD welding’s potential, ensuring efficiency and excellence in every project.
Explore More on Welding Technologies
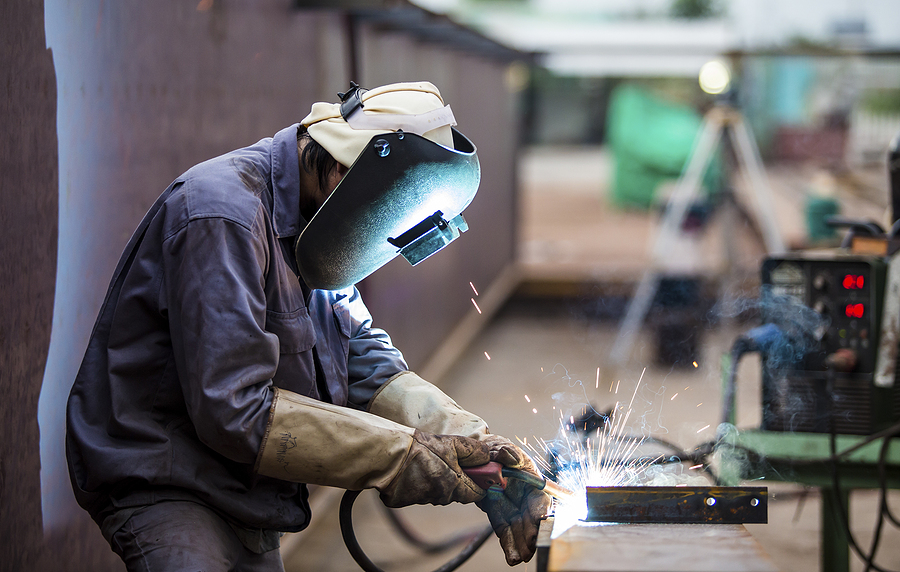
PECo Welding Solutions Expands into MIG and TIG Welding Services
At Process Equipment Company Welding Solutions (PECo), we’re always searching for new ways to serve our community and industry partners. We’re thrilled to announce that PECo is now offering traditional MIG and TIG welding services as part of our growing portfolio....
Ensuring High-Quality Results in Capacitor Discharge Welding: Tips from Industry Experts
Capacitor Discharge (CD) welding is a go-to technique for applications requiring precision bonding, minimal heat distortion, and compatibility with thin or conductive materials. While the process itself is highly efficient, maintaining consistent, high-quality results...
Preparing Metals for Capacitor Discharge Welding: Best Practices for Engineers
Capacitor Discharge (CD) welding is revered for its precision and efficiency, especially in scenarios involving thin or conductive materials. However, the quality of the weld is heavily influenced by how the materials are prepared beforehand. For electrical and...
Understanding Capacitor Discharge Welding: An In-Depth Technical Overview
Capacitor Discharge (CD) welding is a specialized welding technology that plays a pivotal role in various applications where precise, rapid, and high-integrity bonds are required. This process is especially valuable for electrical and structural engineers working with...
Get Expert Guidance on Capacitor Discharge Welding
Reach out to Process Equipment Company today to learn more about our specialized welding services. Whether you need detailed information or a personalized quote, our team is ready to assist you with all your capacitor discharge welding needs.