Capacitor Discharge (CD) welding is revered for its precision and efficiency, especially in scenarios involving thin or conductive materials. However, the quality of the weld is heavily influenced by how the materials are prepared beforehand. For electrical and structural engineers, understanding the nuances of surface preparation, material compatibility, and pre-treatment processes can significantly improve the achievement of optimal results.
This guide provides detailed, practical steps and considerations for ensuring that your metals are ready for the CD welding process.
Why Proper Preparation Matters
Before any welding process, the condition of the metals being joined is critical. For CD welding, even the slightest contamination, surface irregularities, or incompatibilities can compromise the integrity of the weld. Proper preparation ensures:
- Enhanced Electrical Conductivity: A clean, even surface allows for efficient energy transfer during the discharge phase.
- Strong Mechanical Bonds: Preparation eliminates weak spots and improves the fusion between materials.
- Consistent Weld Quality: Properly prepared surfaces reduce variability, ensuring repeatable and high-quality results.
Surface Cleaning Essentials
One of the most important steps in preparing metals for CD welding is cleaning the surfaces that will be welded. Contaminants such as oils, oxidation, dirt, and moisture can weaken the weld or disrupt the discharge process.
Cleaning Methods
Degreasing:
Oils, greases, and other hydrocarbons can be removed using industrial-grade degreasers. Choose a solvent compatible with the material to prevent surface degradation. For example, isopropyl alcohol (IPA) or acetone is commonly used for metals like stainless steel or aluminum.
Mechanical Cleaning:
Abrasive techniques such as sanding, grinding, or using fine-grade stainless-steel brushes can eliminate surface oxides, scales, and rust. For precision applications, opt for micro-abrasive blasting, which removes contaminants without compromising surface geometry.
Chemical Cleaning:
Chemical treatments such as acid etching or alkaline cleaning solutions may be employed to dissolve stubborn oxidation layers or impurities. These should always be conducted under controlled conditions, adhering to safety guidelines.
Plasma Cleaning:
For high-precision or contamination-sensitive applications, plasma cleaning is a viable option. This process uses ionized gas to clean microscopic impurities, ensuring an ultra-clean surface.
Key Considerations When Cleaning
- Ensure that removed contaminants, such as dust from abrasives, are not reintroduced. Post-cleaning, the material should be handled with clean gloves to prevent residue transfer.
- Avoid over-cleaning or damaging the metal surface, which could alter weldability.
Material Compatibility for CD Welding
Not all materials are equally suited for CD welding. Engineers must consider whether the metals being joined possess the necessary electrical and thermal properties for the process.
Compatible Materials
CD welding is highly effective for materials with good electrical conductivity. These include:
- Stainless steel
- Aluminum and its alloys
- Copper and copper alloys
- Brass
Dissimilar Material Welding
When welding dissimilar metals—such as attaching copper busbars to stainless steel—it is essential to assess their thermal and electrical compatibility. Differences in melting points and conductivity require careful adjustment of the capacitor discharge parameters to ensure a strong bond.
Tips for Material Selection:
-
Coatings and Platings:
Some metals come coated with additional layers for corrosion resistance or aesthetic purposes. For CD welding, coatings such as zinc, tin, or nickel must be carefully evaluated and potentially removed from the welding zone, as they can interfere with energy transfer and bond integrity. -
Non-Conductive Layers:
Avoid welding through non-conductive layers like paint or heavy oxide scales. These must be stripped before welding. -
Avoid Brittle Materials:
Materials prone to brittleness under rapid heat changes, such as high-carbon steels, should be reconsidered unless specifically designed for CD welding.
Pre-Treatment Processes
Certain metals require additional pre-treatment to optimize their surface properties for CD welding. These pre-treatments ensure consistent energy distribution and robust bonding.
Annealing
Annealing certain materials, such as stainless steel, can improve ductility and reduce the risk of cracking during the rapid cooling phase.
Surface Passivation
For metals like stainless steel, passivation can help remove surface contaminants such as iron particles left from machining operations. While passivation creates a protective oxide layer, ensure this layer does not interfere with the welding zone.
Texturing
Creating a controlled surface texture may improve the welding process. For example, roughening smooth surfaces ensures better electrical contact between the electrode and the workpiece.
Electrochemical Treatments
Metals like aluminum are often anodized for durability, but the layer must be removed prior to welding. Electrochemical stripping methods can help eliminate the anodized surface without significantly affecting the base metal.
Environmental Factors to Consider
The welding environment can significantly impact weld quality, so it’s vital to maintain a controlled setting throughout the process.
-
Temperature and Humidity:
Excessive humidity can lead to oxidation and moisture contamination. Conduct welding in a dry, climate-controlled environment. -
Dust and Debris:
Minimize airborne particulates. These can settle on prepared metal surfaces or interfere with the electrode. -
Static Charge:
Workspaces should be free of static energy that can disrupt the discharge process. Implement grounding techniques where necessary.
Testing and Verification
Once all preparation steps are complete, testing the metal surfaces and weld setup ensures readiness for fabrication.
Surface Analysis:
Use visual inspections and tools such as profilometers to measure surface roughness. Ensure there are no visible contaminants or irregularities.
Electrical Conductivity Checks:
Test the conductivity of dissimilar metal pairings. Inefficient conduction can indicate a need for additional surface preparation.
Trial and Error:
For critical applications, perform a few test welds on scrap materials to validate pre-treatment processes and the effectiveness of welding parameters.
Final Checklist for Engineers
- Have you removed all contaminants, including dirt, oil, and oxidation?
- Are the materials you’re welding compatible, and have pre-treatment steps been followed as required?
- Is your workspace optimized to reduce environmental variables like dust, humidity, and temperature fluctuations?
- Have you tested your setup to ensure consistent, high-quality welds?
Proper preparation isn’t just a step; it’s the foundation for successful CD welds. By adhering to these best practices, electrical and structural engineers can ensure that every weld meets the highest strength, precision, and reliability standards.
With sound preparation processes in place, your CD welding projects are set for success, paving the way for robust and enduring results. Invest the time to prepare properly—a small effort yields significant returns.
Explore More on Welding Technologies
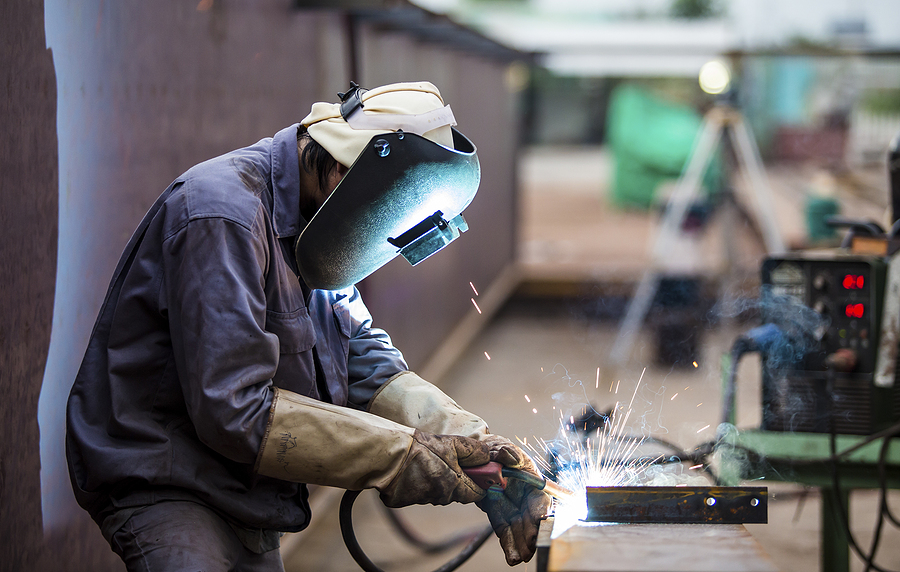
PECo Welding Solutions Expands into MIG and TIG Welding Services
At Process Equipment Company Welding Solutions (PECo), we’re always searching for new ways to serve our community and industry partners. We’re thrilled to announce that PECo is now offering traditional MIG and TIG welding services as part of our growing portfolio....
Capacitor Discharge Welding in Modern Engineering: Applications and Innovations
Capacitor Discharge (CD) welding has become a versatile and efficient welding technique in modern engineering. Its precision, speed, and ability to work with thin materials make it indispensable across industries from electronics to aerospace and construction. Over...
Ensuring High-Quality Results in Capacitor Discharge Welding: Tips from Industry Experts
Capacitor Discharge (CD) welding is a go-to technique for applications requiring precision bonding, minimal heat distortion, and compatibility with thin or conductive materials. While the process itself is highly efficient, maintaining consistent, high-quality results...
Understanding Capacitor Discharge Welding: An In-Depth Technical Overview
Capacitor Discharge (CD) welding is a specialized welding technology that plays a pivotal role in various applications where precise, rapid, and high-integrity bonds are required. This process is especially valuable for electrical and structural engineers working with...
Get Expert Guidance on Capacitor Discharge Welding
Reach out to Process Equipment Company today to learn more about our specialized welding services. Whether you need detailed information or a personalized quote, our team is ready to assist you with all your capacitor discharge welding needs.